Ressources
Key Publications Detail see below
2006
Ind. Eng. Chem. Res.
2005
Comp. Chem. Eng.
2004
Comp. Chem. Eng.
2001
Ind. Eng. Chem. Res.
TransIChemE
Theses (DA+PhD)
PhD L.Cavin [PDF]
DA O. Jankowitsch
DA L.Cavin
Software
Overview
Result Report
Web
Cavin's Home Group Home
ETHZ
|
Abstract
The growing awareness of the civil society for the environment, and the resulting regulations introduced by national states have modified the way chemical industry introduces new products in the market. The resulting profound changes in the process design methodologies have resulted in the integrated process design scheme. This procedure can be defined as the early consideration of significant risks and environmental impacts stemming from the whole lifecycle of the process in all steps of the process design. Methodologies are required to support the design team during the integrated process design.
The development of such a methodology and its related tools is the goal of the research presented here. The focus lies on the implementation of new batch processes in multipurpose production facilities. The method is meant to enable a screening of possible process designs, and assess them according to several objectives.
The methodology is based on a recipe containing a list of tasks to be conducted, and on description of the material streams crossing the system boundaries (raw materials and wastes). In a first iterative phase, the waste streams are analyzed for recycling potentials or for possible treatment problems whose origins can be identified with the help of in-depth analysis tools. Taking those elements into consideration, the recipe can be modified, integrating as well potential recycling tasks. At the last iteration, when the recipe cannot be improved any further, the waste treatment operations needed to handle the waste streams are determined according to financial and ecological objectives for a given waste treatment facility.
In a second phase, the implementation of the resulting recipe in an available production line is addressed. A hybrid superstructure consisting of eligible equipment units and of design heuristics is generated. A multi-objective optimization is conducted to obtain the most promising designs within the superstructure. The objectives are, in order of decreasing priority, the production rate, the number of equipment units used (complexity) and an indicator to favor “top-down” designs. This optimization is conducted with a meta-heuristic method: the Tabu Search. Its parameters as well as some algorithm options have been tested and tuned in order to achieve a high probability of finding the optimal design within a low computational time for a broad range of cases. The resulting design is an allocation of equipment units for each task of the recipe.
The second phase can be repeated for several production lines, and a higher level indicator (e.g. the production costs) can be used for selecting the most promising production line. With the selection of the waste treatment path, the production line and the design, the implementation of a new process into an existing facility is completed.
Numerous case studies of industrial relevance have been used to test the methodology. Ranked panels of promising designs have been generated with corresponding indicators in about one hour of computations. The various indicators allow a discussion and an evaluation of the designs according to other criteria not directly used in the optimization (e.g. batch size). Discussions with experts have shown that both the process designs and the waste treatment paths obtained correspond to high-quality implementations – and in some case studies, they have even been proven to be optimal with side considerations. This makes the methodology powerful for numerous tasks, ranging from screening projects, in order to address “go-no go” decisions, to the detailed implementation of a new process in existing waste treatment and production facilities.
| Presentations
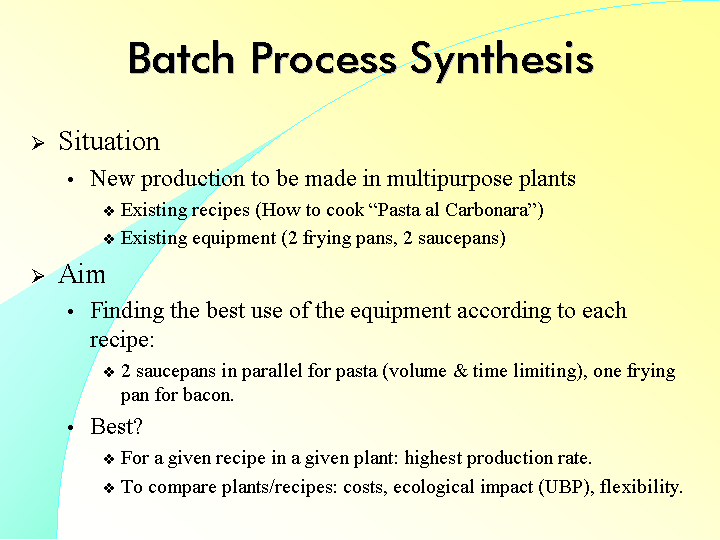
Concept (3 slides) Two minutes teaser
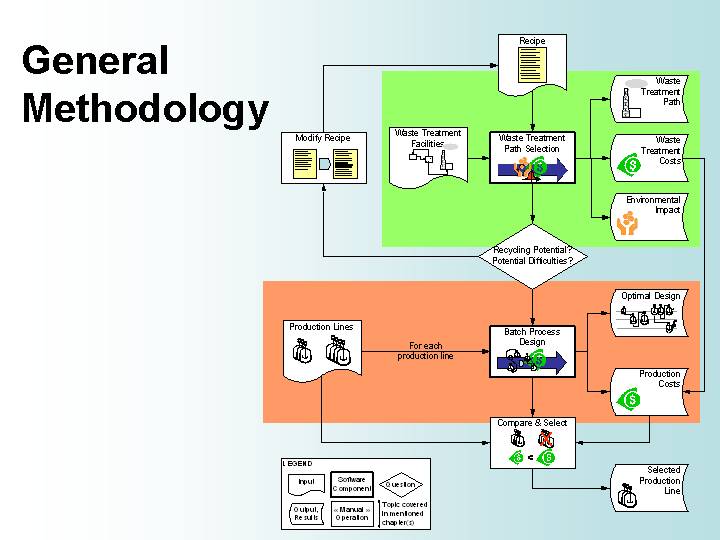
ETHZ, Dec. 2002 Final PhD Presentation - Extracts - The whole picture
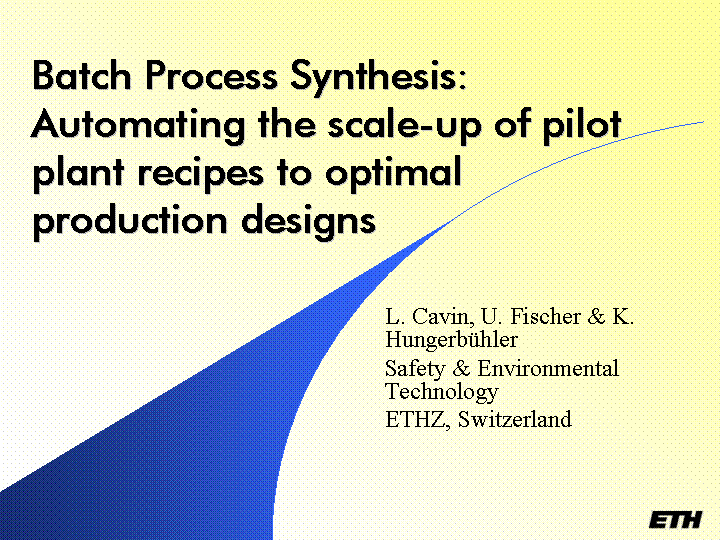
AIChE Meeting 2002 Nov. 2002, Indianapolis, IN, USA Batch Process Design Component
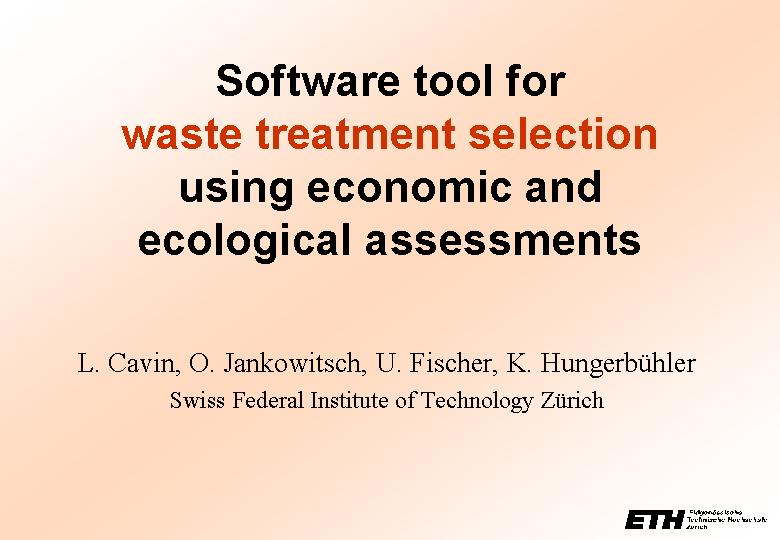
ESCAPE-10 May 2000, Florence, Italy Waste Treatment Component
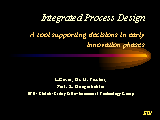
AspenWorld 2000 February 2000, Orlando, FL, USA (An outdated presentation not available online anymore).
|